What Is The Process Of Barite?
Barite is a mineral composed of barium sulfate, the color of it is white or colorless. Barite usually shows in crystal, the gap filler in sedimentary rock. This mineral can also exist in limestone, dolomite, or sandstone. It is easy to identify barite ore through its weight. Therefore, barite ore often uses as a weighing agent in drilling mud.
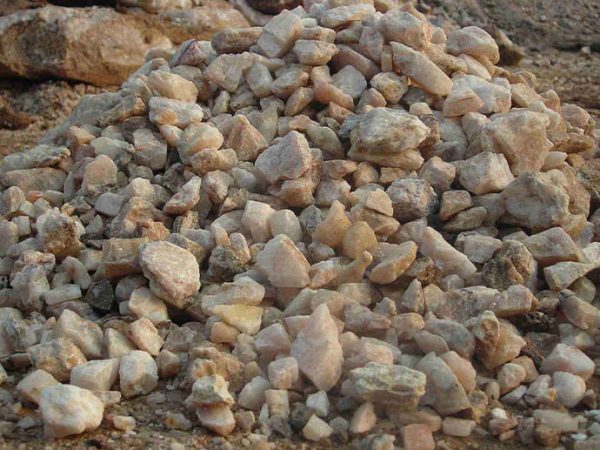
Crystalline minerals have many other uses, including adjusting the thickness of fillers in the paint, improving the stability and color brightness of paint; Used in paper fibers to obtain a higher density of paper; Used as a weighting filler for rubber mudguards and other rubber materials that require additional weight; Medical X-ray shielding agents, etc. With the development of the barite ore process, the demand for barite mining equipment is also increasing.
Barite Processing Flow
- Crushing Process
Barite is brittle and fragile, during the crushing process, we recommend the jaw crusher instead of an impact crusher or hammer crusher to crush barite to produce a large amount of fine barite ore. The raw ore after primary crushing reaches a better crushing effect.
- Screening Process
The size of the barite ore after crushing is uneven, and the beneficiation equipment generally has its own required input size and size range. Therefore, the crushed barite ore after screening can optimize the following separation process, which improves the separation efficiency and separation indicators of the separating equipment.
- Classify Process
The material under the screen will go to a spiral classifier or other classified equipment to obtain concentrate and tailings.
- Dehydration Process
After being sorted by a spiral classifier, the concentrate and tailings discharged contain significant moisture. Dewatering measures are generally required to reduce the moisture content of the concentrate and remove excess moisture to return to the circulating pool, reducing the quantity consumption of the circulating water system.
Baryte has wide applications, It needs to be ground into powder or extracted the barium sulfate, so it needs to grind into powder for use, and there will need a drying machine and grinding machine for barite processing.
- Rotary Drum Dryer
When the drum rotary dryer works, the barite goes to the hopper and then to the feeding end of the barite dryer by the vibrating feeder, and smoothly enters the cylinder through the inclined feeding pipe. The cylinder rotates slowly during operation and has an inclination angle with the horizontal line. Baryte enters the cylinder from the high end and slowly moves towards the low position under gravity. At the same time, the heat carrier is introduced from the lower part and impacts towards the high end, making reverse contact with barite, and complete drying baryte process in connection between the two. In addition, the cylinder body with a board can lift and sprinkle barite materials, increasing the contact area between baryte and heat carrier, and improving the drying rate.
Performance characteristics
- Low investment cost: On the one hand, the equipment adopts a centralized electrical control system, which has a high degree of automation and does not require too many human resources, resulting in low labor costs; On the other hand, the equipment has a relatively small volume, lightweight, convenient transportation, and with low infrastructure costs. Therefore, the investment cost of this device is relatively low, saving a lot of labor power and material investment for the enterprise.
- High capacity: the design of a lifting plate device improves the passing volume of barite materials, makes materials fully in contact with heat sources, and improves the drying efficiency of barite.
- Energy conservation and consumption reduction: The cylinder has good insulation function, low heat loss, high utilization rate, low electricity consumption, and low fuel waste, achieving the production goal of energy conservation and consumption reduction.
- Reliable quality: The cylinder and other devices adopt advanced wear-resistant materials, which have excellent wear resistance and high-temperature resistance. The operation process is very stable and can withstand long-term tests. The quality is super reliable, and the service life is super long.
- Green and environmentally friendly: The unique design of the noise reduction and dust prevention device reduces dust and noise levels during the drying process of the equipment, achieving the goal of being green and environmentally friendly.
- Grinding Mill
The qualified barite powder is sent to the warehouse by bucket elevator and then to the barite mill for grinding by electromagnetic vibration feeder. The classifier screens the barite powder. The cyclone collector collects the qualified products, and the unqualified products return to the barite grinding mill for grinding.
Working principle
- During the operation of ultrafine grinding, The main equipment motor through the reducer drives the main bearing and each rotary table.
- Under the action of centrifugal force, the material is moved to the edge of the rotary table and falls into the grinding chamber. The material is repeatedly ground by rollers in the grinding chamber. Then the material falls into multiple layers, continuously crushing and grinding into micro powder.
- The high-pressure blower continuously sucks in air from the grinder. On the other hand, the airflow with crushed materials is carried to the classifier, and the high-speed impeller of the classifier will screen the airflow. The unqualified particle size decreases and returns to the grinder for re-grinding. The qualified particle size is mixed with air and enters the cyclone dust collector.
- Most qualified powder will descend from the bottom discharge valve. A small portion of the fine powder moves with the airflow to the dust collector and adheres to the surface of the filter bag. Meanwhile, due to the instantaneous injection of high-pressure gas controlled by the pulse valve, the fine powder attached to the cover falls off due to the sudden vibration of the filter bag.
- The above two batches of materials are transported by the bottom conveyor and packaged with finished powder. In addition, the filtered clean air will eventually discharge from the outlet of the muffler.
Advantage
- The output is 40% higher than other mills.
- The high utilization rate of wear-resistant materials: 2-5 years.
- Adjustable particle size: 150-3000 mesh.
- High safety and reliability. The grinder is designed strictly and will not damage the machine due to loose screws.
- The closed system of green ideal equipment
Barite Processing Plant Cases
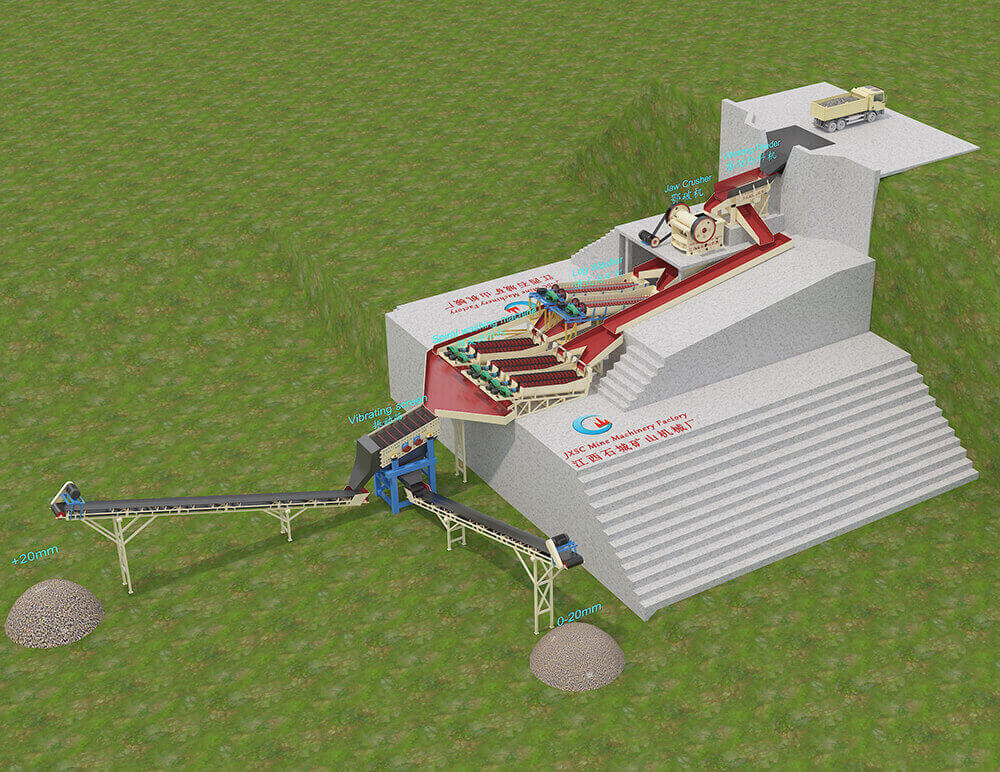
- This setup is a barite processing plant configured with a vibrating grizzly feeder, jaw crusher, log washer, spiral sand washer, vibrating screen, and belt conveyors.
- The materials under the grizzly bar of the vibrating feeder go to 2 spiral sand washers through the material guide chute, the material above the grizzly bar feed to the jaw crusher.
- The discharged material of the jaw crusher enters the two spiral log washers, and the spiral classifier out materials feed into the spiral sand washer.
- The overflow of the spiral ore washer guide to the vibrating screen, and the discharging materials of the three spiral sand washers are all fed into the vibrating screen.
- The vibrating screen sieve out two kinds of finished products with different particle sizes, 0-20mm, and materials over 20mm.
Eastman is a professional mining machine manufacturer in China. We supply all kinds of mining machines to fit your different applications. After getting your requests, we will design the flow chart for free and suggest suitable mining machines for you. If you are interested in our products, don’t hesitate to inquire for more information!