Application of Sand Making Machine in Crushing Process of Concentrator
With the global warming, the voice of efficient emission reduction is rising day by day. The consumption cost of beneficiation energy has attracted the attention of the management organization as well as the selected grade. Crushing screening and grinding classification of stone production line is a main link in the beneficiation production process. Reducing ore crushing energy consumption and improving crushing efficiency have always been widely valued. According to the practice of metal mines in China, the crushing process flow of concentrators in mines that have been put into operation is roughly as follows: two-stage and one closed-circuit crushing process flow, three stage open circuit crushing process flow, three stage and one closed-circuit process flow, new three-stage and one closed-circuit process flow, four stage and one closed-circuit process flow. If the production scale of mines is less than 500t per day, basically, the crushing process uses two-stage one closed-circuit crushing process flow or three-stage one closed-circuit process flow.
The particle size of the final products of the two processes(two-stage one closed-circuit crushing process flow & three-stage one closed-circuit process flow) is relatively large, generally about 25mm. This particle size enters the grinding process, which increases the grinding load and production cost.
The specific ideas are as follows: the crushing part of the general concentrator adopts two-stage one closed-circuit crushing process flow or two-stage three-stage one closed-circuit crushing process flow. No matter what crushing process is adopted, the actual maximum particle size of grinding materials is more than 15mm-25mm, or even greater.
Our idea is: after the crushed raw ore is classified by vibrating screen, the ore on the screen will be finely treated, instead of returning to two-stage crushing or three-stage crushing and crushing again. Instead, the “sand making machine” is used for processing and open circuit discharge.
The working principle of the sand making machine is as follows: the material enters the sand making machine from the feed hopper and is divided into two parts through the distributor. One part enters the high-speed rotating impeller from the middle of the distributor and is rapidly accelerated in the impeller, with an acceleration of hundreds of times the gravitational acceleration, and then ejected from the flow channel, First, a part of the ore falling from the distributor is impacted and broken, and then it is impacted on the material lining in the vortex branch chamber together, which is rebounded by the ore lining. Because the material emitted from the impeller channel forms a continuous material curtain, such an ore is subject to repeated impact, friction, grinding and crushing in the vortex crushing chamber; The crushed materials are discharged from the lower discharge port in the south. In the whole crushing process, the ores impact and crush each other without direct contact with metal components, prolonging the time of mechanical wear.
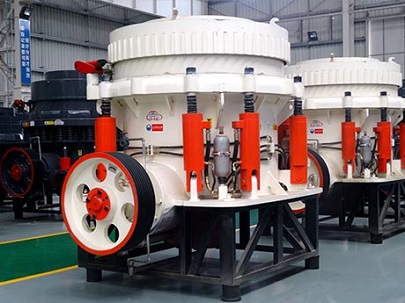
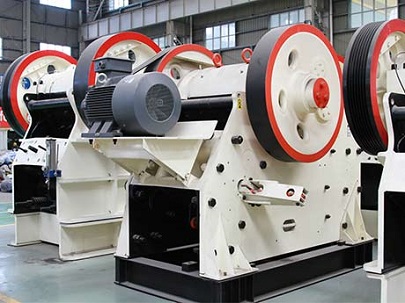
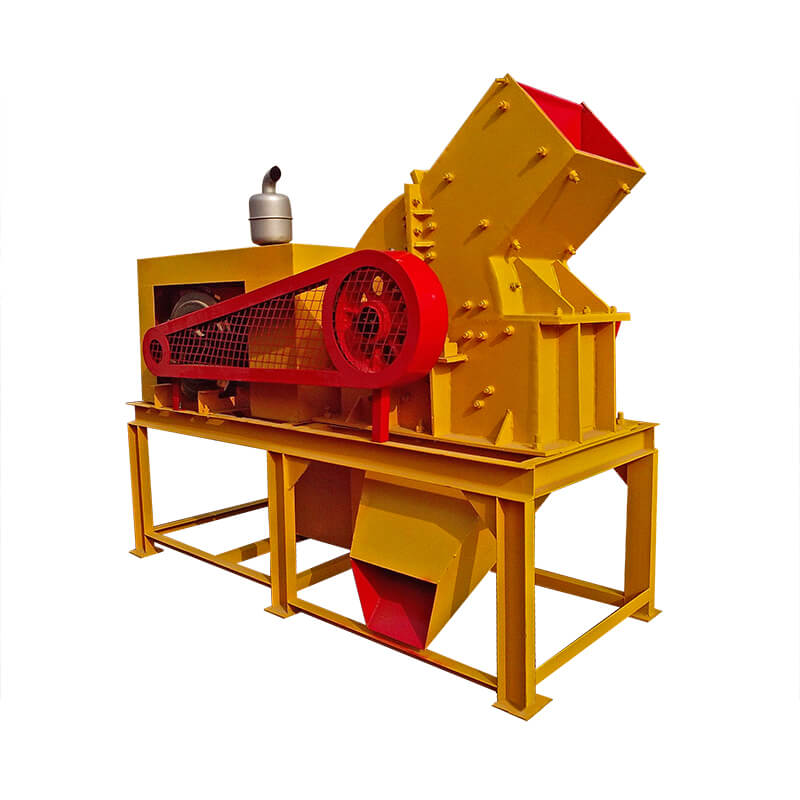
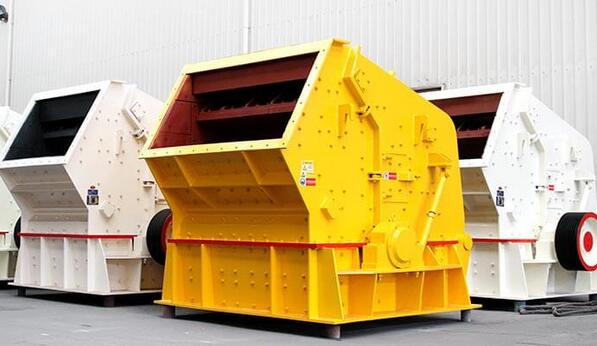
The ingenious air flow self circulation in the vortex chamber eliminates dust pollution. It is assumed that other fine crushing equipment is adopted. The hammer crusher, hammer head and lining plate in the crusher consume a lot. They are replaced frequently, have low hourly output, high power consumption, difficult maintenance, long maintenance time and low equipment operation rate. The consumption of hammer head and lining plate is amazing. The ore processed by the equipment and the ore under the screen are transported to the powder bin (also known as buffer bin) by belt conveyor for grinding. According to the data summarized by previous research departments, the coarser the ore feeding, due to the longer grinding time, the more power consumption and lower productivity to grind it to the specified fineness, and the change of ore feeding particle size has a great impact on the productivity of the grinder. The relative productivity of the grinding machine calculated according to the newly formed -0.074mm level usually increases with the decrease of feed particle size, but the increase range decreases with the thinning of products. The increase range of coarse grinding is larger than that of fine grinding, and heterogeneous ore is more obvious than homogeneous ore.
Taking a concentrator with a daily processing capacity of 100t as an example, the particle size of crushed ore before grinding is mostly about 25mm, which greatly reduces the efficiency of the mill. Because the mill is fine grinding equipment and the coarse crushing efficiency of the mill is low, the grinding efficiency is very low when the ore of 25mm is ground below 8m. At this time, the power consumption of 1 ton of ore is about 30kwh. If the advanced crushing process is used, the ore has been crushed to the fine grade and the product content is higher. At this time, the power consumption of grinding 1T ore by the mill is only about 11 degrees. The method is to add a “sand making machine” on the raw material coarse crushing system to reduce the feeding particle size of the mill from 25mm to 10mm, and the proportion of – 5mm is doubled compared with the original; The power consumption of fine crusher for crushing 1 ton of ore is about 5kwh. Change to before grinding. Fine crushing equipment is used for the fine crushing of ore so that the power consumption of 1t ore in crushing and grinding systems can be reduced by about 10kwh. In this way, tens of thousands of kWh of electric energy are saved every year, which not only increases the economic benefits of the mine but also contributes to environmental protection. Moreover, the use of pre-grinding fine crushing equipment will also reduce a lot of steel consumption.
Crushing equipment recommend Jaw crusher, impact crusher, hammer crusher, cone crusher, ball mill, etc., Eastmancrushing is a professional crushing equipment manufacturer in China. We have 36 years’ produce experience in the mining industry. We supply free consultation and flow design services. If you have such requirements, please feel free to contact us. Tell me your mining ore, feeding size, and output discharge particle size, our engineer will according to your budget and needs to design the flow chart and match appropriate equipment. This will help to maximize the benefits of your production line.