Energy Saving and Consumption Reduction of Cement Mine Emission Reduction
About Energy Saving
The energy-saving of the mine runs through all production processes. Here we only focus on the energy-saving problem of using continuous and semi continuous production, using less or no cars and replacing oil with electricity.
With the development of China’s economy, the increasing demand for liquid fuel, and the increasing shortage of international oil, oil saving in mine production has been urgently mentioned in front of us. Since the reform and opening up in the 1980s, many of us have visited and investigated abroad, and were deeply impressed by the high efficiency of continuous production with mobile crushing. Our peers hope to be applied in China, but because of its high price, it has always become an elusive luxury.
As far as the mining industry is concerned, with the expansion of the scale of open-pit mining, the traditional mining technology requires many large excavators and transportation vehicles, which makes the organization and production very complicated and overburdened. The application of continuous and semi continuous mining technology can be relieved, and remarkable energy-saving effect and economic benefits can be achieved.
As for the mining technology, some literatures call the production of wheel bucket excavator belt conveyor waste dumper as continuous technology; The production of single bucket excavator truck crusher belt conveyor is called semi continuous process; The production of single bucket excavator truck is called intermittent process. The continuous process is only applicable to soft rock that can be excavated directly, and its application range is limited. Hard rock and semi hard rock are more suitable for semi continuous process. The crushing station, the key equipment of semi continuous process, can be set in the pit or on the surface, which can be fixed, semi fixed or mobile.
Now we study our own problems. Limestone, the main raw material for cement production, is mostly hard rock and semi-hard rock. They are difficult to dig directly with wheel bucket shovel. We need to study the production process according to our own characteristics. The symbolic measure of replacing oil with electricity is to use less or no cars, and the replacement method is to use more belt conveyors to transport ore. The multi-purpose belt conveyor needs to move the crusher into the mining site. Therefore, studying the form and location of crushing station is the key to which production process should be adopted in our cement mine.
The emergence of mobile crushing in the mining site dates back to the 1950s. It was first applied in the limestone mine of a cement plant in West Germany, and then gradually extended to coal mines and metal open-pit mines. This is because limestone is sedimentary rock, which has the characteristics of thick ore bed, uniform quality, simple mining method, light crushing equipment and high output. It is easier to place on the crawler walking car body than other crushing equipment. The mobile crusher follows the excavator to crush large ore into gravel and then transport it with belt conveyor, which can save automobile transportation, greatly save manpower and fuel and reduce the ore production cost. The production technology of using belt conveyor to transport ore out after crushing in the stope has been rapidly expanded all over the world since the 1970s. There have been many types of moving modes and various types of crushers to adapt to different service conditions. Its single machine capacity has been nearly 10000 tons / hour.
Mobile Crusher
Category and Performance of Mobile Crusher
Mobile crusher, more accurately, should be called mobile crushing station, because it is equipped with feeding and discharging devices and supporting facilities in addition to crusher. According to different mobile functions, it can be divided into full mobile, semi mobile and portable. The service conditions of the three crushing stations are different, which can only be selected after considering many aspects. Full mobile crushing station is also called self-propelled crushing station. According to the walking mode, it can be divided into crawler type, rubber wheel type and walking type. The flexibility of the three walking modes is different, so their uses are also different. The crawler type can work with the excavator, but the body is bulky, restricted and the capacity is small. At present, the known maximum capacity is 1000t / h. Rubber wheel and walking type can not follow the excavator, they can only work under relatively fixed conditions. Their production capacity is large, and many crushing stations with a capacity of 2000 ~ 3000t / h are in use. A basic feature of the self-propelled crushing station is that it is a single unit with complete functions. The feeding and discharging are on the same platform, which is referred to as “flat feeding and flat discharging”. At present, some manufacturers also call the “upper in and flat out” crushing station as self-propelled crushing station, which will actually cause confusion in understanding.
The semi mobile crushing station needs external force to move. Some can feed and discharge materials on the same platform, others need to feed on the previous platform, and the host stands on the platform to discharge materials (hereinafter referred to as “flat in and flat out” and “upper in and flat out”). The former can be used in any accessible position, while the latter needs to use a step with certain restrictions on its position. The crushing station of “upper inlet and horizontal outlet” is more suitable for large mines because it uses the height of one step, increases the volume of silo and shortens the feeder. At present, the largest semi mobile crushing station in the world is a copper mine in Chile, with a capacity of 9600t / h.
Semi mobile crushing station includes crushing station on track, crushing station on flat trailer and piggyback crushing station. Large semi mobile crushing stations are generally relocated by piggyback. In order to facilitate relocation, it is often separated into several monomers. For example, the silo and feeder form one monomer, the crusher is another monomer, and the discharge belt conveyor is one monomer, so as to reduce the weight of each relocation unit. Due to the high price and low utilization rate of piggyback trucks, some mines are also relocated in other ways.
Semi mobile crushing station is a floating frame on the ground, does not need a solid concrete foundation, and its bearing capacity to the ground is generally not less than 250kPa.
Movable crushing station, also known as assembled crushing station, is a structure between fixed and mobile crushing stations, which is used when relocation is not frequent (more than 2 ~ 3 years). They can be disassembled into several large pieces, and their size and weight meet the lifting capacity of the crane and the bearing capacity of the trailer. The time spent for one relocation depends on the preparation before the event, the degree of disassembly, the length of the relocation distance and the organization. A limestone crushing station in Mexico has a capacity of 6000t / h and a total weight of 420t. The relocation cycle is no less than 2 ~ 3 years. The relocation takes 12 ~ 15 days.
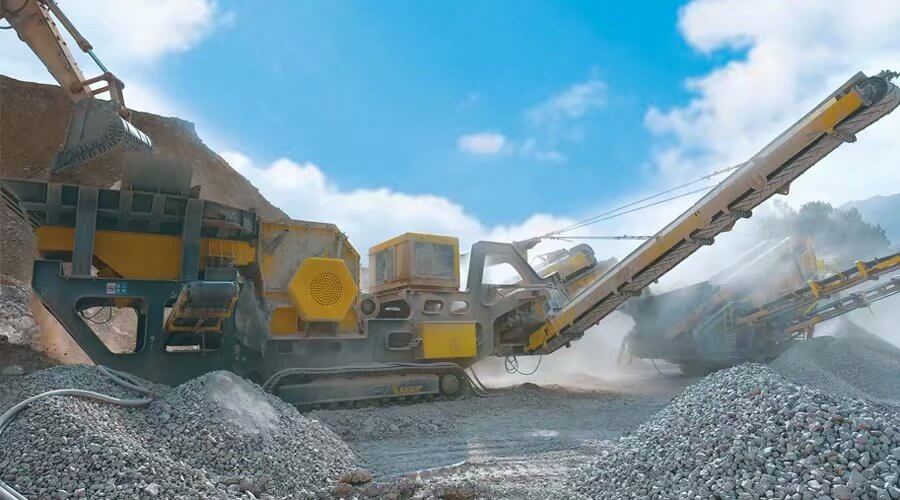
Application Methods of Various Mobile Crushing Stations
According to the characteristics of limestone mines for cement, the basic crushing station types and applicable conditions of three crushing modes are put forward for reference. If only one crushing station is used. If the scale is large, it is proposed to adopt two sets of crushing stations, which is easy to realize in quality matching, the application scope of traveling type and surrounding loading type will be expanded. When the specific height of the mine is large and the ore body rock stratum is stable, an internal chute is dug, and a fixed crushing station is set underground. After the ore is crushed, it is also an energy-saving production process to make full use of potential energy, and the crushing station does not need to be relocated, which is more convenient. This production process has been applied in many cement plants in China for a long time, so it will not be repeated here.
Consumption Reduction of Crushing
The crushing machinery is also worn in the process of processing ore. In order to minimize the loss of parts, first, it is necessary to adhere to the scientific selection of models; Second, rational use and material selection.
At present, the common situation in China is to ignore this work when building factories, and rush into the bidding process without arranging necessary manpower for substantive investigation and research, which is quite blind. Once the type selection is improper, the serious will cause the factory’s long-term production passivity, and the light will also cause frequent consumption.
The basis of scientific selection of models is to have a scientific understanding of the origin of processed raw materials. It includes the understanding of the physical and mechanical properties of the ore and entrainment in each layer of the deposit, sampling and processing test, and then make the correct model selection in combination with the local natural climate conditions and the requirements of the factory production process on the ore inlet and outlet particle size, etc.
There are many types of crushers with different working principles, so the characteristics of the machine are very different, which needs to be studied in combination with the characteristics of the ore in the place of use (including the differences of ore characteristics in different horizons). When there are multiple selection schemes, the final selection conclusion should be considered according to the one-time investment and long-term consumption.
The consumption of broken materials is related to many factors. Taking the hammer as an example, its service life is related to the following four factors:
- the physical properties of minerals and the properties of companion organisms (abrasiveness to metals, soil content, moisture, viscoplasticity, compressive strength, etc.)
- Rationality of the internal structure of the machine;
- Correctness of hammer head material selection and manufacturing quality;
- Operation method.
The first is objective existence and congenital. We need to have a correct understanding in advance.
The second item indicates the internal treatment of the machine to prevent abnormal excessive wear in order to adapt to the nature and process requirements of the processed materials.
The third issue is material selection. At present, the hammer heads of single-stage Hammer Crushers include high manganese steel (including alloy high manganese steel, ultra-high manganese steel added with alloy elements, and alloy high manganese steel with surfacing wear-resistant layer on the striking surface); Medium carbon alloy steel (including double hardness hammer head with impact section hardness hrc55-58, matrix 39 and impact toughness > 240j); Bimetallic composite (head is high chromium cast iron, HRC > 61, handle is chromium molybdenum alloy steel, hb225 ~ 310); High manganese steel embedded with cemented carbide. For brittle limestone with medium hardness, high manganese steel hammers are mainly used when the abrasivity is not high. When the abrasivity is high or there is more sandy soil mixed in the material, the cold work hardening layer of high manganese steel hammers is difficult to form and maintain, so the effect is not good and should not be used. The effect of using medium carbon alloy steel hammer head for coal and gypsum is also better than that of high manganese steel hammer head.
The fourth item is the use and operation method of crusher. The adjustment of the grate and the flanging of the hammer head are timely or not, and the effect is very different. At present, some factories do not even flanging or adjustment, and allow them to rub in the excessive space accumulation layer formed between the grate and the rotor, and the service life of wear-resistant materials will not be long. Therefore, it is necessary to establish a system and use it carefully in order to prolong the service life of the parts.