Sand Making Plant Equipment Selection And Noise Problems
With the vigorous development of infrastructure, the demand for sand and gravel aggregates is also increasing, and the machinery and equipment of sand making production lines are also developing rapidly. Among them, crushers, screening machines, etc. are the hardest hit areas of noise pollution, which has caused a series of difficulties for the production of our customers. To choose reasonable equipment, but also to solve this noise problem, we must adopt a comprehensive management approach.
Selection of sand making plant equipment
1. Crushing equipment: jaw crusher, cone crusher, impact crusher, mobile crusher
The focus of the sand making production line is the equipment, among which the crushing of raw materials and the selection of special crusher products are the overall equipment matching, the focus and key of the production line construction. In terms of meeting the higher standard needs of production line construction, it is also a particularly important equipment in the process of achieving assured crushing function guarantee and effect, and it is more in line with the key points of production efficiency guarantee and quality.
2. Sand-making equipment: impact sand-making machine, vertical shaft sand-making machine, vertical compound crusher
The mechanical equipment for sand making is to carry out the purpose of forming sand. The sand making machine is the core equipment of the whole sand and gravel production line, and it is used to make sand for gravel. After the stone passes through the sand making machine, the finished product is of excellent quality, rounded in shape and meets the grading standard.
3. Screening equipment: vibrating screen, high-frequency screen
In addition to the application of crushing and sand making, the terminal equipment is screening, which can ensure the specification matching of finished products and ensure that more qualified products can be screened. It is a good choice in the actual situation of production and application. Currently, the commonly used screening equipment has adjustable specifications and standards, which can improve production accuracy.
4. Auxiliary equipment: vibrating feeder, belt conveyor
The material needs to enter the crusher uniformly, quantitatively and continuously through the vibrating feeder, which can improve the crushing efficiency. The belt conveyor is a continuous conveying material equipment with the characteristics of continuous conveying, reliability and convenience, long conveying distance, low energy consumption, large conveying capacity, and environmental protection.
Sand Making Plant Flow
One. Crushing stage
This mainly includes coarse crushing and medium and fine crushing production and processing. The applied mechanical equipment is carried out in the form of jaw crusher + cone crusher / impact crusher. The actual selection of mechanical equipment is mainly based on the characteristics of raw materials. In the crushing process, facilities such as vibrating feeder and vibrating screening machine are also needed to assist the smooth completion of production.
Two. Sand making stage
The crushed material is sent to the impact crusher through the belt conveyor for sand making work. The sand produced by this equipment is of high quality and good grain shape, which meets the standard requirements of construction sand, and there are many types of equipment for different Sand making requirements can also use different machinery and equipment.
Three. Sand washing stage
In order to ensure the quality of the finished sand products, sand washing is required for the materials after the sand making machine is processed. The machine-made sand screened by the vibrating screen is cleaned in the sand washing machine to obtain clean machine-made sand, which is then sent to the finished product pile.
The sand-making production line has the advantages of high automation level, low operating cost, high crushing rate, environmental protection and energy saving, large production capacity, less environmental pollution, and simple maintenance.
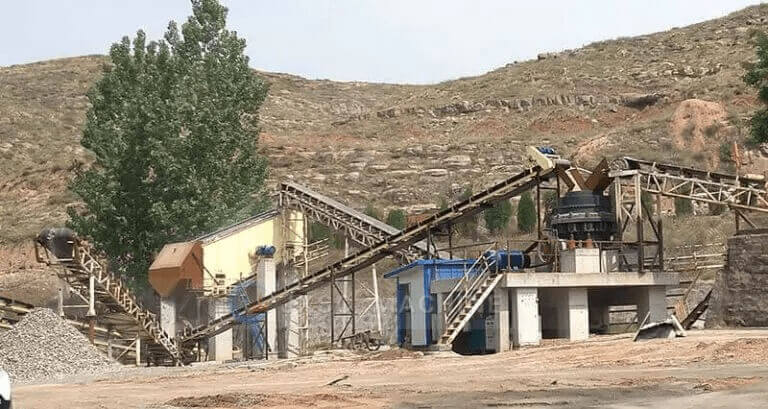
How to solve the noise problem
1. Reasonable choice of terrain
Sound is called noise only when it affects people’s production and life. Therefore, when we choose the address of the gravel production line, we must pay attention to staying away from areas where people gather, especially when designing and planning. Make flexible use of terrain and features, such as hillsides, hills, woods and other natural environments, and block noise transmission channels according to local conditions.
2. Sound insulation treatment method
It is very necessary to make full use of the basic principle of sound transmission and adopt targeted sound insulation and noise reduction methods to block noise. Sound insulation materials are an efficient way to insulate and reduce noise from media transmission.
Sound insulation materials should be made of high-density materials, using the basic principle of sound transmission. In cross-density transmission, the higher the density difference between the two media, the worse the actual effect of sound transmission. Use reflection and blocking methods to adjust sound transmission. , in order to achieve the effect of sound insulation and noise reduction.
The construction unit must consider the actual location of the noise source of the production line equipment, set up a soundproof shed in the heavily polluted area, and use soundproof materials to seal the roof and surrounding walls.
3. Parts inspection method
Some sounds can be avoided or greatly reduced from the root. For example, in the work of key equipment such as crushers and screening machines, any loose parts may cause additional vibration. And the additional vibration happens to be one of the main sources of noise.
In this regard, all parts should be checked and fastened before the equipment is in operation; rubber springs are used to replace the vibrating springs of the screening machine; rubber sieve plates or polyurethane sieve plates with relatively low impact noise are used to replace traditional perforated steel sieve plates and steel woven screen; add proper amount of lubricating grease to the moving parts of the equipment to reduce the frictional resistance of the relative moving parts of the machine and equipment, and reduce the noise caused by friction.
4. Special material handling method
The sieving machine is where the noise is more serious, which has a lot to do with its physical properties. The screening machine is composed of steel parts, and the representative ones are beams, screen surfaces, side plates, reinforcement plates, etc. During the operation, these steel components will also vibrate, which will cause noise pollution. Moreover, due to the complexity of the working system of the screening equipment itself, these noises also have the characteristics of multiple sound sources and high sound levels.
For this, damping springs and damping rubber can be installed between the screen boxes of the screening machine. As a material consumed by converting mechanical vibration into heat energy, damping material also plays a good role in sound insulation and noise reduction. At the same time, the sound-absorbing body can also be suspended in the air in the sound-proof booth, making full use of the sound-absorbing function of the material of the sound-absorbing body, absorbing the reflected sound in the sound-proof booth, and further reducing noise pollution.
The finished product regulations play a decisive role in the composition of the entire production line. River (cobblestone) pebbles, bluestone, granite, basalt, limestone, sandstone and even waste rock, construction waste, etc. can be used as raw materials for sand and gravel plants. As a result, raw materials from local mines can be preferentially selected, thereby reducing transportation costs. The machine-made sandstone made of pebbles, bluestone, granite and other mine raw materials has high hardness and good grain shape, which is suitable for bridges, high-rise buildings and other industries that require high sandstone aggregates. Sand and gravel made of construction waste and waste rock are usually of poor hardness, and can be used as filling materials for the construction of roads and railways. Rocks are widely used after mining and processing, making money while realizing an environmentally friendly sand making production line.
The specific choice of sand making plant equipment mainly depends on the type and hardness of the material, the size of the finished product, the site and the actual demand, etc. Contact our professional engineers for consultation! Get the factory prices!