Rock Gold Mining Equipment And Technologies
The gold is extracted from gold mines, and it is not easy to get pure gold from gold mines. It needs a series of beneficiation equipment to process the rock gold to high-value gold. From ore to gold, the value has doubled several times, so many users are interested in mining gold. As we all know, gold is valuable, but its content in gold ore is low. It is necessary to crush the gold ore, finely grind it, and then adopt gravity separation and flotation methods to enrich or separate the gold. What are the commonly used beneficiation methods, techniques, and equipment in gold mining?
Rock Gold Mining Equipment and Process Flow
Rock gold process usually include stages as follows.
- Crushing stage
The equipment used in the crushing stage includes jaw crushers and cone crushers. Both machines are suitable for crushing high-hardness stones such as gold ore. Firstly, the jaw crusher is for roughly crushing the gold ore, and then the cone crusher is for intermediate crushing.
- Grinding stage
The equipment for the grinding stage is a ball mill to grind the gold ore from the cone crusher. The feed particle size is 20-25mm, and the discharge particle size is 0.074-0.89mm.
- Gold ore gravity separation stage
Gravity separation adopts the mineral density differential beneficiation. It uses equipment such as shaking tables, spiral chutes, jig separators, and hydrocyclones.
- Gold flotation stage
The flotation method is a mineral processing method that uses the different physical and chemical properties of mineral surfaces to separate minerals, and commonly used equipment includes flotation machines.
The specific beneficiation equipment needs to be determined based on the properties of the gold ore, beneficiation scale, and process flow.
Rock gold mining equipment
The complete set of gold ore selection equipment mainly includes crushing equipment (jaw crusher, cone crusher), ball mill, spiral classifier, shaking table, mixing tank, spiral chute, flotation machine, thickener, leaching tank, and auxiliary equipment (vibration feeder, circular vibrating screen, conveyor), etc.
Rock Gold Mining Process
- After the first stage of crushing, the raw ore enters the double-layer vibrating screen for screening. The upper layer products are further crushed and combined with the middle layer products for the secondary crushing. The second-stage crushed products are returned and combined with the first-stage crushed products for further screening.
- The product from the vibrating screen enters the ball mill and forms a closed circuit grinding with the classification mechanism. The classification overflows after classification by the cyclone and enters the second stage ball mill for further grinding, and then forms a closed circuit grinding with the hydrocyclone.
- The cyclone overflow is subject to preferential flotation, and its foam products become the concentrate products after secondary and tertiary cleaning. The tailings after preferential flotation are subject to the separation flow of primary roughing, primary cleaning, secondary cleaning, tertiary cleaning, and primary scavenging.
- The tailings from the primary cleaning and the foam products enter the hydrocyclone for re-classification and re-separation. The secondary and primary cleaning constitute closed circuit separation.
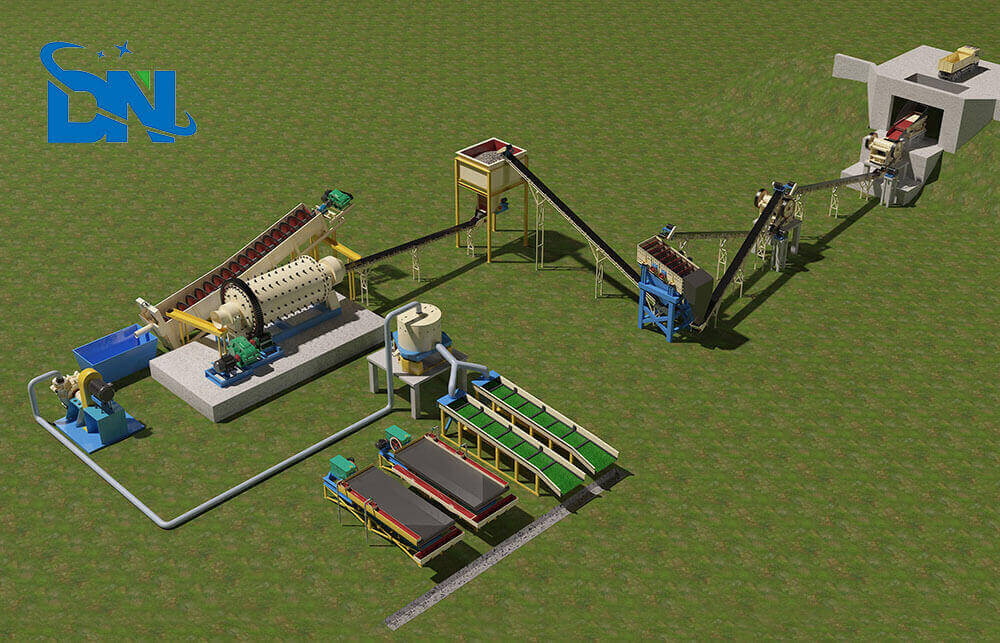
Rock Gold Processing Method
Crushing and grinding
The crushing process uses a jaw crusher for coarse crushing, a standard cone crusher for medium crushing, a short-head cone crusher, and a pair of roller crushers for fine crushing. Most small and medium-sized gold beneficiation plants adopt a two-stage closed-loop crushing process, while large gold beneficiation plants adopt a three-stage closed-loop crushing process. To increase production and equipment utilization, ore dressing plants generally follow the principle of more crushing and less grinding, reducing the particle size of the ore entering the grinding process.
Gravity Separation
Gravity separation is a method based on the difference in mineral density to separate the gold. The equipment includes spiral chutes, shaking tables, jig machines, and hydrocyclones.
Flotation Separation
80% of gold beneficiation plants use flotation to select gold, and the produced concentrate goes to non-ferrous smelters for processing. Due to the increasing development of cyanide-based gold extraction and the need for enterprises to improve economic efficiency and reduce concentrate transportation losses, they often adopt on-site treatment. The flotation process has made significant progress and occupies an essential position in gold selection production.
Chemical separation
The main chemical selection methods include the mercury mixed extraction and the cyanide extraction processes. The mixed mercury method for gold extraction is an ancient process, which is simple and economical, suitable for recovering coarse-grained monomeric gold. However, it causes significant environmental pollution. It was gradually replaced by gravity separation, flotation, and cyanide methods for gold extraction.
The cyanide-based gold extraction process includes several processes, including cyanide leaching, washing and filtration of leached ore slurry, extraction of gold from cyanide solution or cyanide slurry, and smelting of final products.
Leaching
Low-grade oxidized ore accounts for a proportion, and using conventional cyanide extraction technology to treat this type of ore is not economically cost-effective while using heap leaching production technology still has economic benefits.
Technology for gold mining
- Mineral resource assessment technology: The potential quantity and grade of gold resources need to be evaluated to determine the mining value and feasibility of the deposit.
- Geological exploration technology including geological surveying, geochemical exploration, and other technologies. By analyzing the structure, composition, and distribution of ore, to find the location and scale of mineral deposits.
- Mining engineering technology includes geological exploration, mine design, beneficiation plant design, construction, production, and other aspects of technology to ensure the safety, efficiency, and sustainability of the whole mining process.
- Mining machinery and equipment: such as drilling, mining, transportation, mineral processing equipment, etc.
- Mining environmental protection equipment such as wastewater treatment, exhaust gas treatment, mining area restoration machines, etc. To protect the environment and reduce the impact of mining areas on the surrounding environment.
- Human resources and management: It is necessary to have human resources such as engineers, technicians, and operators with professional knowledge and skills, as well as management institutions and systems in mining management, safety monitoring, and other aspects.
Mining gold requires the use of crushing, grinding, and separation equipment. The specific type of equipment depends on the actual production situation. The selection of a gold ore selection plant is a multifaceted and comprehensive system engineering. Therefore, it is necessary to adhere to the principles of adapting to local conditions, facilitating production, fully coordinating, saving costs, and achieving high production efficiency for multi-dimensional consideration.
Eastman is a professional mining equipment manufacturer with 38 years of rich experience in the mining construction industry. We can also provide lab equipment. Welcome to consult our professional team to get factory prices. According to your situation and product requirements, we will design a complete sand-crushing production line flow chart and provide an accurate quotation.