Hard Alloy Sand Production Process
Hard alloy sand is essential in various industrial applications, including foundries, construction, and abrasive products. It is known for its durability and resistance to wear. Hard alloy sand consists of tungsten carbide, silicon carbide, and other hard metals. The production process, the equipment, and quality control measures is crucial for high-quality hard alloy sand. We will explore how to make hard alloy sand, the equipment required, and best practices to optimize production.
What is Hard Allioy Sand?
Hard alloy sand refers to fine aggregates enriched with hard alloy particles, making them suitable for high-stress applications. The composition often includes materials such as:
- Silicon Carbide (SiC) is ideal for abrasives and high-performance applications. It is renowned for its hardness and thermal stability.
- Tungsten Carbide (WC): Extremely hard and wear-resistant, often used in cutting tools and drilling applications.
- Alumina (Al₂O₃): Provides good hardness and chemical resistance and is commonly used in ceramics and abrasives.
These materials are valued for their ability to withstand extreme conditions, making hard alloy sand a preferred choice in demanding industries.
Steps to Produce Hard Alloy Sand
Producing hard alloy sand involves several critical steps. Let’s delve into each step of the production process:
-
Raw Material Sourcing
The first step in producing hard alloy sand is sourcing high-quality raw materials. The quality of the raw materials directly impacts the final product.
- Material Selection: Choose high-purity silicon carbide, tungsten carbide, or alumina, depending on the intended application. Silicon carbide is often chosen for abrasive applications, while tungsten carbide is for its superior hardness in cutting tools.
- Supplier Verification: Ensure that suppliers provide materials that meet industry standards. Conducting audits and quality checks on the raw materials can prevent issues.
-
Crushing and Grinding
Crushing and grinding the raw material to achieve the desired particle size and distribution.
- Crushing: Use a jaw or impact crusher to break down larger chunks of hard alloy materials. This initial crushing reduces the size of the material, making it easier to grind.
- Grinding: The material is ground to a fine powder by a ball mill or roller mill after crushing. The grinding process is crucial for achieving the desired particle size, typically between 0.1 to 0.5 mm for hard alloy sand.
- Ball Mill: This equipment uses steel balls to grind materials in a rotating drum, providing efficient size reduction.
- Roller Mill: This type uses cylindrical rollers to crush and grind the material, offering a finer product with less energy consumption.
Screening
Screening is essential for separating particles based on size and ensuring uniformity in the final product.
- Vibrating Screen: Utilize a vibrating screen to classify the ground material into different sizes. This equipment allows only the desired particle size while larger particles back for further grinding.
- Size Distribution: Maintaining a consistent particle size distribution is critical for applications like casting and abrasives, where uniformity affects performance.
Washing
Washing the sand is crucial to remove impurities, such as clay, dust, and other contaminants that can affect the quality of the hard alloy sand.
- Washing Equipment: Use a sand washer or hydrocyclone to clean the sand thoroughly. The washing process should ensure the final product is free from unwanted materials that could compromise its performance.
- Water Quality: Use clean water for washing to prevent introducing additional impurities. Regular monitoring of water quality can ensure consistency in the washing process.
Drying
After washing, dry the hard alloy sand to remove excess moisture.
- Drying Equipment: Use a rotary dryer or fluidized bed dryer. Maintaining the moisture content is critical, as too much moisture can lead to issues in applications like casting and abrasives.
- Rotary Dryer: This equipment uses hot air to evaporate moisture, efficiently drying the sand as it tumbles.
- Fluidized Bed Dryer: This technology allows sand to be suspended in hot air, promoting even drying and minimizing the risk of overheating.
Quality Control and Testing
Quality control is crucial throughout production to ensure the hard alloy sand meets industry standards.
- Testing: Regular testing of physical properties such as hardness, particle size distribution, and chemical composition is necessary to ensure compliance with specifications.
- Hardness Test: Perform the Mohs hardness test or Vickers hardness test To determine the hardness level of the material.
- Sieve Analysis: This test assesses particle size distribution, ensuring that the sand meets the required specifications for its intended use.
- Chemical Analysis: Conducting chemical analysis helps confirm that the composition of the hard alloy sand meets the necessary standards for performance and safety.
- Adjustments: Based on test results, adjustments may be needed in the crushing, washing, or mixing processes to achieve the desired quality.
Packaging and Storage
After the production process, pack and store the sand to maintain quality.
- Packaging: Use durable bags or bulk containers to package the sand for transportation. Proper packaging helps protect the sand from moisture and contamination during storage and transport.
- Storage: Store the packaged sand in a dry, clean area to maintain its quality until it is ready for use.
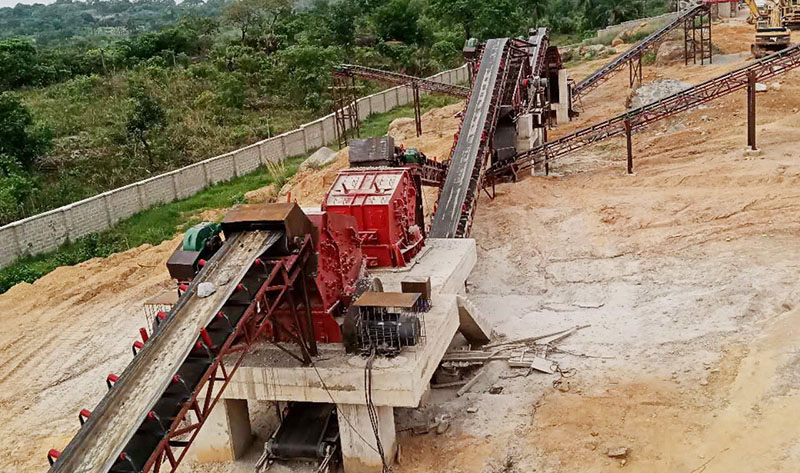
Hard Alloy Sand Process Equipment
It requires several key pieces of equipment to produce hard alloy sand efficiently.
- Jaw Crusher: Primary crusher for larger raw material chunks.
- Impact Crusher: Secondary crusher for further size reduction after primary crushing.
- Ball Mill or Roller Mill: Grinding the crushed material into a fine powder.
- Vibrating Screen: To separate particles based on size and ensure uniformity.
- Sand Washer or Hydrocyclone: Clean the sand and remove impurities.
- Dryer (Rotary or Fluidized Bed): Remove moisture from the washed sand.
- Quality Control Equipment: This includes hardness testers, sieves, and chemical analysis equipment to ensure the sand meets the required specifications.
Optimizing Hard Alloy Sand Production
To enhance the efficiency and quality of hard alloy sand production, consider the following best practices:
Regular Maintenance: Keep maintenance to ensure optimal performance and minimize downtime. Implementing a routine maintenance schedule can prevent unexpected failures.
- Quality Raw Materials: Always source high-quality raw materials to ensure the best performance of the final product. Building strong relationships with reliable suppliers can help maintain a consistent quality of raw materials.
- Monitor Environmental Conditions: Be aware of environmental factors such as humidity and temperature, which can affect drying and mixing processes. Adjusting operations based on weather conditions can help maintain product quality.
- Implement Automation: Consider automating the mixing and quality control processes to improve consistency and reduce labor costs. Automation can also enhance precision in measuring and mixing materials.
- Training Staff: Ensure that staff operating the equipment are well-trained and understand the importance of each step in the production process. Continuous training programs can help keep employees updated on best practices and new technologies.
Conclusion
Producing hard alloy sand involves a systematic process that includes sourcing raw materials, crushing, grinding, screening, washing, drying, and conducting quality control tests. By investing in high-quality machinery and adhering to strict quality control measures, manufacturers can produce hard alloy sand that meets the needs of various industrial applications.
As industries continue to evolve, the demand for high-quality hard alloy sand will remain strong, making it a valuable product for manufacturers. If you’re considering entering the hard alloy sand production market or upgrading your existing processes, understanding these steps and the equipment involved will help you achieve optimal results.
Eastman is a professional mining equipment manufacturer with 38 years of rich experience in the mining construction industry. We can also provide lab equipment. Welcome to consult our professional team to get factory prices. According to your situation and product requirements, we will design a complete sand-crushing production line flow chart and provide an accurate quotation.